Etching
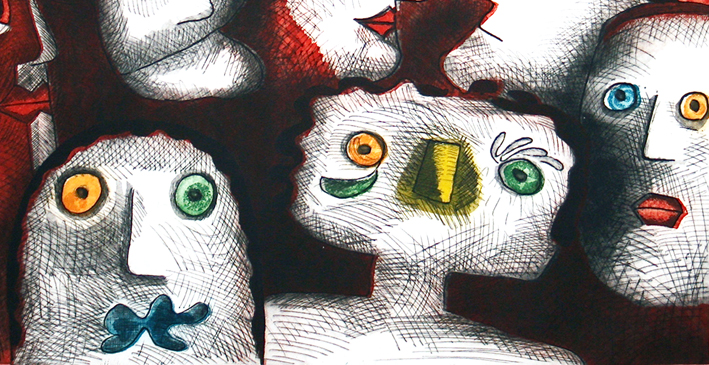
Detail of Folla by Enrico Baj. Etching, 100 copies, 1985 – 80 x 120 cm
Aquafort etching is an ancient method of creating art prints. The artist scratches off the surface of a metal plate (usually copper or zinc) covered with a waxy ground with a pointed etching needle that he uses like a pen to trace a drawing that will be printed reversed. The plate is then dipped in a bath of nitric acid. The acid “bites” into the metal, where it is exposed, leaving behind lines sunk into the plate. In order to obtain darker lines the plate can be dipped in acid again.
The plate is inked all over, and then the ink is wiped off the surface, leaving only the ink in the etched lines. The plate is then put through a high-pressure printing press together with a sheet of paper (often moistened). The paper picks up the ink from the etched lines, making a print.
The plate is inked all over, and then the ink is wiped off the surface, leaving only the ink in the etched lines. The plate is then put through a high-pressure printing press together with a sheet of paper (often moistened). The paper picks up the ink from the etched lines, making a print.
Aquatint
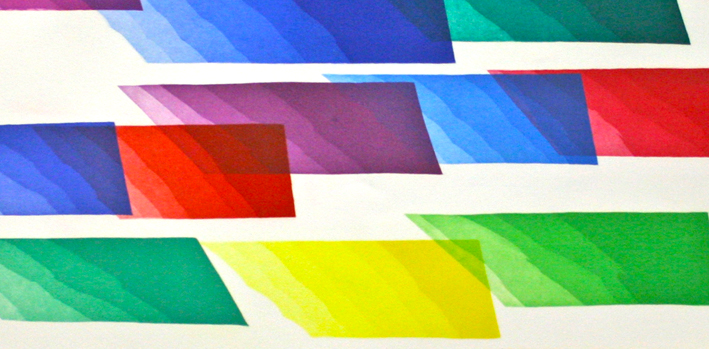
Detail of Color Fax, by Piero Dorazio. Aquatint, 100 copies, 1990 - 78 x 96 cm
This printing process named “aquatint” consists in the granulation of a metal plate, coated with wax. The texture is created by dropping grains of salt on the matrix which stick to the heated plate. The grains of salt will be cleaned off, thus leaving small interstices where the acid will penetrate.
Effective shades of light and dark can be achieved, simply by varying the time of immersion and by coating the blank areas with a greasy varnish.
Aquatint is usually combined with aquafort, since the printing process is the same, on the same matrix or on different ones, that will be printed with different colour inks in order to obtain the desired image.
Effective shades of light and dark can be achieved, simply by varying the time of immersion and by coating the blank areas with a greasy varnish.
Aquatint is usually combined with aquafort, since the printing process is the same, on the same matrix or on different ones, that will be printed with different colour inks in order to obtain the desired image.
Lithograph
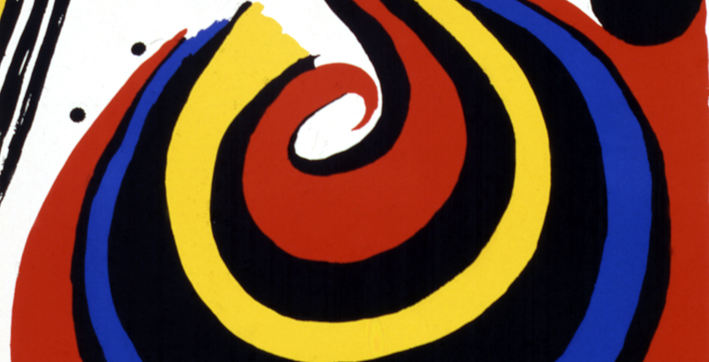
Detail of Girandola by Alexander Calder. Lithograph, 100 copies, 1972 - 75,5 x 56 cm
Lithography, from Greek ”lithos” (stone) and ”graféin” (to write), is a method of printing using a stone (limestone) having a smooth surface. This printing process works on the principle that grease and water repel each other.
The artist draws on a stone with a greasy crayon or ink and then covers the stone with a thin film of water.
Ink is applied to a grease-treated image on the flat printing surface; non-image (blank) areas, which hold moisture, repel the lithographic ink. This inked surface is then printed directly on paper perfectly reproducing the artist’s drawing, by means of a rubber cylinder. The oily ink will stick to the greasy image but not to the water-covered areas.
The same process may be used today by using metal plates – zinc or steel – treated with granulation, in order to slightly roughen the stone plate – repelling greasy ink – on the non-image areas.The artist can draw on different stones or plates with various colours and print them on the same paper, in order to obtain colour prints.
The artist draws on a stone with a greasy crayon or ink and then covers the stone with a thin film of water.
Ink is applied to a grease-treated image on the flat printing surface; non-image (blank) areas, which hold moisture, repel the lithographic ink. This inked surface is then printed directly on paper perfectly reproducing the artist’s drawing, by means of a rubber cylinder. The oily ink will stick to the greasy image but not to the water-covered areas.
The same process may be used today by using metal plates – zinc or steel – treated with granulation, in order to slightly roughen the stone plate – repelling greasy ink – on the non-image areas.The artist can draw on different stones or plates with various colours and print them on the same paper, in order to obtain colour prints.
Silk-screen printing
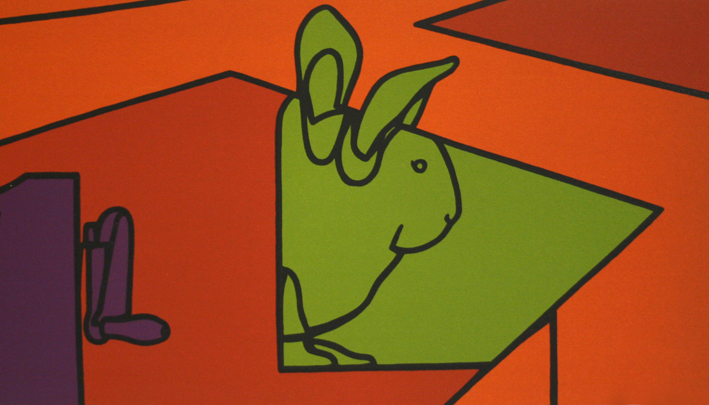
Detail of Coniglio by Valerio Adami. Screen printing, 200 copies + XX, 1975 - paper: 41 x 67 cm - print: 28 x 57 cm
This ancient printing technique first appeared in China where silk was used in the process, prior to the invention of polyester mesh. It is a stencil technique that employs fabric stretched tight on a screen support frame.
A stencil is created on the screen by applying a “blockout” (glue, paper, hand-cut film, or photosensitive emulsion or gelatin film) to all non-image areas. Ink is then applied to the entire screen using a squeegee which forces the ink to pass through the open area of the stencil onto paper or other material.
As with screen printing can be obtained flat, rich and compact colours, this technique is particularly suitable to two-dimensional images. A number of screens can be used to produce a multicoloured image or design.
A stencil is created on the screen by applying a “blockout” (glue, paper, hand-cut film, or photosensitive emulsion or gelatin film) to all non-image areas. Ink is then applied to the entire screen using a squeegee which forces the ink to pass through the open area of the stencil onto paper or other material.
As with screen printing can be obtained flat, rich and compact colours, this technique is particularly suitable to two-dimensional images. A number of screens can be used to produce a multicoloured image or design.